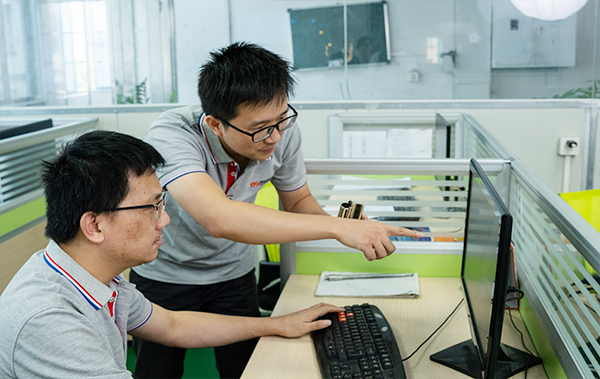
Rapid prototyping is a group of techniques used to quickly fabricate a scale model of a physical
part or assembly
using three-dimensional computer aided design (CAD) data.
Our rapid prototyping service includes CNC machining, polyurethane vacuum casting, sheet
metal fabrication, SLA&SLS. Various materials and post surface finishes are available.
Where the design closely matches the proposed finished product it is said to be a high
fidelity prototype, During the research and development stage, it is more flexible for your
engineers.
With the rapid prototyping techniques, you can manufacture parts or the products to test for the component fit and function in a faster and low cost way. Based on the analysis results before putting into the market, it can help you effectively save time and costs. A lot of our customers need to manufacture a component quickly to verify the feasibility of a design or a product.
Rapid Prototyping Advantages
Faster Speed and Shorter Delivery Time
Excellent Surface Quality
High Dimensional Accuracy Can be up to±0.01mm
Unlimited Design Space
Reduced Costs
High Degree of Automation in Forming Process
Test a Full Range of Designs
Precise Entity Replication
Customization
Better Market Visibility
What can we do in WeLead?
SLA(StereoLithography) and Selective Laser Sintering (SLS)
3D Printing Rapid Prototype (SLA-Stereolithography, SLS-Selective laser sintering)
SLA and SLS are revolutionary rapid technologies, objects can be of almost any shape or geometry and typically are produced using digital model data from a 3D model.
3D printing builds a three-dimensional object from computer-aided design (CAD) model, usually by successively adding material layer by layer.
Each layer will reach to 0.1mm thin, which makes the part surface looks much smoothly without paying too much extra cost.
Surface Finish: Sanding smooth, Painting, Printing etc.
Polyurethane Casting (Vacuum Casting)
Polyurethane Casting is also called vacuum casting, which is an excellent and cost
effective option for prototype testing before proceed to tool making.
To better control the tolerance and cost, SLA master model is the choice to make the identical cavity. By pouring liquid silicon material into an aluminum box then dry to be solid, after demoulding a silicon mold is done. It is the most cost saving process for the complex part feature. If high polish or clear surface is required, CNC machining PMMA master model is the option.
Surface Finish: Texture, Sandblasting, Color matching, Pad Printing etc.